The science of Inventory management relies on good, accurate data and a consistent process to ensure you optimise your organisation’s inventory.
If any of these scenarios apply to you, consider investing in optimising your inventory:
- High value, slow moving item with no indication of business criticality
- Regular stock outs leading to excessive production delays.
- Items missing information in the CMMS leading to planners and technicians wasted time trying to find an item.
- Overall cost of inventory management to the organisation is high.
- Cost of expediting items out of stock is excessively high.
Examples from my experience include:
UK Factory - Many different analogue chart recorder models were replaced over time but the paper charts in the storeroom filled up a section of the storeroom and they could have been sold with the recorders.
As the maintenance manager in an Australian factory, I found that the store area was a small mezzanine above the workshop. a lot of the items in the mezzanine seem to have been bought when the machinery was bought and were covered in dust.
In a larger organisation with a fully manned store managing many components for both operations and maintenance. The inventory management team would routinely dispose of any item that had not been moved over a 2-year period. In one instance, a high value item was disposed of only to find that Maintenance needs one for a major overhaul job four weeks later.
From a personal perspective, I have had my car off the road for 3 days since a key part had to be shipped from Sydney to my repairer.
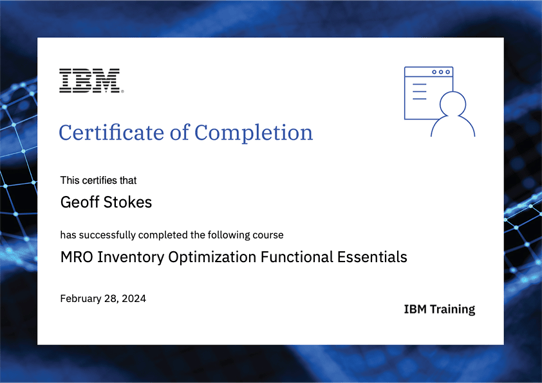
Geoff's certificate in MRO Inventory Optimization Functional Essentials
I have no doubt that many of you will have similar experiences and taken some steps to rectify the situation in your organisation.
A comprehensive analysis and assessment will require a large amount of people’s time to ensure the Inventory is optimised to suits your business objectives.
Optimised inventory can be summarised as
The strategic management and control of stock levels which meet the objectives of Maximum efficiency, Minimised risk and the avoidance of wasteful surplus.
In an MRO organisation, this summary suggests these objectives can be viewed as
- Minimised unplanned asset downtime
- Efficient planning of all Maintenance and inspection work
- Increased technician working time due to materials being planned and on hand.
- Efficient procurement processes for restocking stores based on demand.
Is Inventory Optimisation something to be implemented in your organisation and where do you start?
To focus on quick wins, look at some Inventory related data in core areas of the business:
- Do you have an Inventory Management Policy or process and is it up to date?
- Is your Item master and associated data complete?
- Are Items registered in related storerooms and has the inventory item data needed for optimisation been populated?
- Are Items included in the Asset spares list and the Job Plan templates, leading to demand driven item management?
- How often are small quantities of the same item purchased annually?
- How often are Purchase orders expedited to meet an urgent need?
- Do you quantify technician time wasted searching for parts?
- Is there enough demand to address the costs of living with these types of scenarios?
Addressing these data and process shortfalls requires an investment in time to deliver results as there are so many potential areas to address.
A quick response to resolve high priority and urgent issues could contain these steps:
- Identify the shortfalls in your master data, the Item master and Inventory records.
- Ensure the routine demand for materials is added to all programmed work plans.
- From here forecasting tools in the CMMS can highlight the annual (or longer) demand profile for these items.
- They can also identify issues with the existing Reorder point (ROP) and Economic quantity (EOQ) values.
- Assess the purchasing history to identify Vendor lead times and cost history.
- If the items are grouped, select the group which would benefit most from optimisation and use these to pilot the program.
These are a few of many approaches to start your journey to optimise inventory. There are many other tactics which can be applied to integrate inventory optimisation into the core business practices.
Should you wish to explore optimisation further, BPD Zenith consultants can provide further insights on your data, identifying focus areas with you and assisting with the preparation of an Inventory optimisation Business case.
